Mould powders were initially used in bottom-pouring, ingot casting in Belgium in 1958 but its application continuous casting commenced from 1963. Casting powders are preferred over oil because of their better thermal insulation to the steel surface which allowed steelmakers to operate with significantly lower superheat and at the same time providing better control of the horizontal heat extracted from the shell. Moreover, the liquid slag pool over the liquid steel surface prevents the steel from coming in contact with the atmosphere thereby preventing oxidation. The slag pool also absorbs some of the non-metallic inclusions (e.g. Al2O3) present in the molten steel.
These initial mould powders were based on fly ash, which is basically a waste product from power stations and contained a high percentage of SiO2, Al2O3, and unburnt carbon. CaO and various other fluxes (e.g. Na2O and CaF2) were also added to it. The powders heat up as form a slag pool which acts as a reservoir of liquid slag which infiltrates between the shell and the copper mould wall at a time when the mould is descending (which occurs throughout the negative time period and early part of positive strip time). This liquid slag partially solidifies to form a slag film which consists of a solid layer that is 1–2 mm thick and a liquid layer that is 0.1 mm thick. The initial slag film formed consists primarily of glassy phases owing to the high cooling rate but over time the fraction of crystalline phases (fcrys) gradually increases until it reaches a steady-state value. With the increasing demand for better quality control, fly ash powders got gradually replaced by synthetic mould powders.
The amount of lubrication provided to the steel shell is determined by the amount of thickness of the liquid slag film (dl). Whereas the thickness of the solid layer (ds) and fraction of crystalline phases fcrys determines the amount of heat extracted from the shell.
The level of lubrication provided is described by the powder consumption which again depends on the surface area of the shell, Qs in kg (slag) m−2 (of mould), which is equal to q.dl where q is the density of liquid slag.
The melting rate is controlled by adjusting the quantity and size of the free carbon in the powder. The typical values are for slabs and billets (with large and small surface areas) are 4% and 25% respectively.
The constituents of mould powders can be divided into four classes:
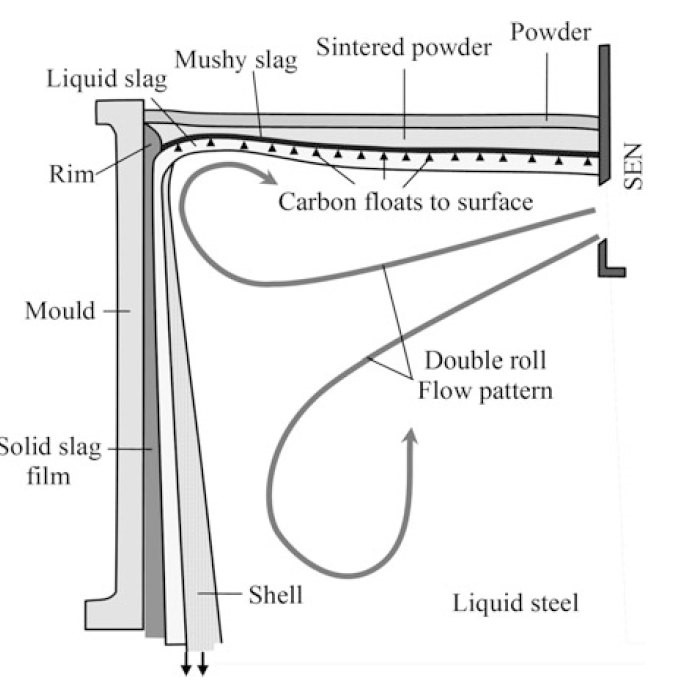
(i) network formers (SiO2, Al2O3),
(ii) network breakers (CaO, MgO),
(iii) Fluxes (Na2O, K2O, CaF2, B2O3) and (iv) Carbon particles with different sources and sizes (e.g. lampblack, coke breeze, etc.). In addition, mould powders contain (i) some minerals which are present as carbonates which decompose on heating giving off CO2(g)and (ii) some impurities present in the minerals (e.g. TiO2, FeO).
Physical properties (such as viscosity and thermal conductivity) of the liquid slag formed are dependent upon the degree of polymerisation of the slag which increases with increasing SiO2 and Al2O3 contents and decreasing the amounts of CaO, MgO, CaF2and Na2O. The basicity (%CaO/%SiO2) is a useful measure of the de-polymerisation. Glassy slags are highly polymerised but increasing basicity results in both decreasing polymerisation and increasing crystallisation of the slag (i.e. fcrys increases).
Mould Powder Behaviour in the Mould
The powder bed at the top comprises three layers, namely, powder, sintered and liquid layers.
The reactions and chain of events that occur in the following sequence (i.e. as the mould powder heats up):
(i) moisture, if any, in the flux evaporates at the top of the bed.
(ii) At a temperature of around 500 °C, carbonates (such as CaCO3 and Na2CO3) decompose to form oxide and CO2(g)
(iii) Carbon in the powder reacts with oxygen and CO2 (g) to form CO (g) in those regions of the bed where the temperatures are between 500 and 900 °C; these reactions are exothermic.
(iv) In this temperature range, the mineral particles also start to sinter.
(v) Finally, the solid slag begins to melt at temperatures above 900 °C and forms
a liquid slag pool; any remaining carbon particles float in this pool.
This slag pool serves as a reservoir of molten slag for subsequent infiltration into the shell/mould gap and a pool depth of at least 10 mm is to be ensured for satisfactory infiltration of liquid slag.
The slag pool carries out important functions such as:
(a) It prevents oxidation of the steel by preventing its contact with the atmosphere.
(b) Serves as a reservoir for a constant stream of liquid slag to lubricate the shell throughout the length of the mould.
(c) It keeps the floating carbon particles away from the shell and thereby reduces C-pick-up by the steel.
Slag Film
The slag film is important because it is our main tool to control the shell. The slag film controls both the lubrication and the heat transfer from the shell, and so it determines the characteristics of the shell (e.g. shell length and thickness).
Hence, the characteristics of the slag film are the key to the success of the casting process. Lubrication is inversely related to the liquid friction force (F1).

where A is the surface area of the shell (or mould), η is the slag viscosity and Vm is the velocity of the mould. Thus, liquid friction decreases with decreasing values for mould surface area, viscosity, and (Vm− Vc) and increasing slag film thickness.
The crystalline phases reflect and scatter radiant energy leaving the shell; thus heat extracted decreases with increasing fcrys and with increasing crystal size. Crystallisation is often associated with shrinkage owing to the higher density of the crystals compared to the glasses. This shrinkage results in the formation of (i) porosity in the slag film and (ii) an interfacial thermal resistance (associated with an “air or gas gap”) at the Cu/slag interface. Increasing porosity and resistance decreases the total heat transfer.
In conventional mould powders containing fluorides cuspidine (3CaO_2SiO2_CaF2 denoted as, C3S2Fl) crystals initially precipitate near the mould side of the slag film because of the undercooling of the liquid. However, large dendritic crystals form near the high temperature on the shell side of the slag film as because the crystal growth is promoted by high temperatures.
Slag Rim
Slag films are formed by the infiltration of molten slag into the shell/mould channel. Slag rims are their equivalent which is formed near the meniscus area by the “painting” mechanism as the mould travels through the powder, sinter, and liquid slag layers. The contents of the slag film reflect this and contain unmelted mould powder, sinter, glassy carbon and molten slag. An examination of a rim revealed it contained a series of layers bounded by Na2O-rich frozen liquid which provided evidence for the painting mechanism. The low melting, Na2O-rich liquid was considered to act as glue. The carbon comes from both the powder bed and from the C-rich layer formed by carbon particles floating at the top of the slag pool. The slag rim is thought to act as a piston and pushes liquid slag into the mould/strand channel.
Highly crystalline slag rims tend to fracture easily and can
(i) cause depressions in the surface of the steel [36–38], (ii) get trapped in the shell/mould channel and block off slag infiltration which results in sticker breakouts and
(iii) create false alarms in the sticker detection system. Thus the formation of ropes can be harmful to continuous casting.
Casting Conditions
The mould powder composition is chosen as per the casting conditions; these include (i) the casting speed, (ii) the mould dimensions, (iii) the oscillation characteristics, (iv) the nature of the steel being cast and (v) the Ar flow rate.
Metal Flow
The metal flow pattern is an important factor in continuous casting. The double-roll pattern is the preferred pattern in continuous casting. The single-roll flow pattern tends to decrease meniscus temperature which can sometimes lead to meniscus freezing. Asymmetric flows can lead to high levels of slag entrapment.
At high-casting speeds, turbulent metal flow occurs which results in high metal velocities and the formation of both standing waves on the metal/slag interface. These conditions increase the chances of slag entrapment. The height of the standing waves also determines the longitudinal cracking in the product. Electromagnetic braking has been found useful in retarding the velocity of the metal leaving the SEN.
Mould Dimensions
the lubrication supplied by the liquid slag increases with increasing surface area of the mould and the required powder consumption is in the hierarchy, Qs slabs >Qs blooms >Qs billets.
Oscillation Characteristics
Most steel plants operate with a fixed negative strip time. In order to maintain same value of negative strip the depending factors such as frequency and stroke are adjusted. Plant trial data have indicated that powder consumption increases with decreasing frequency and stroke.
Steel Grade
Longitudinal cracks tend to occur when the horizontal heat flux exceeds the certain critical value which can result in an overly thick shell. The shells of peritectic grades are more susceptible to cracking because of the 4% differences in thermal shrinkage coefficients for austenite and ferrite. Thus longitudinal cracking is avoided by ensuring thin, uniform shell; which is achieved by creating a thick, crystalline, slag film (i.e. with high values of break temperature Tbr and fcrys).
Sticker breakouts are associated with the formation of a thin, weak shell which can be minimized by forming a thick, strong shell and is achieved with a high qhor by creating a glassy, thin, slag film (i.e. with low values of Tbr and fcrys). Thus, the nature of steel affects the required properties of the mould slag.
Ar Flow Rate
Excessive Ar flow rates (>5 l/min) can transform a double-roll flow pattern in the steel to single-roll flow pattern, which provides less satisfactory casting conditions.
Fluctuations in the Process
The turbulence increases with increasing casting speed. The turbulence can be controlled by (i) optimising parameters, like the immersion depth of the SEN and SEN port design and (ii) using electromagnetic devices to reduce metal flow turbulence and to homogenise temperatures and steel composition.
Physical Properties of Mould Slags
The mould slag must provide adequate lubrication which depends on the fluidity (or and the break temperature. The key properties for the control of the heat flux (qhor) are Tbr (which determines the thickness of the solid layer of the slag film) and fcrys, the fraction crystalline phase in the slag film. Apart from that thermal conductivities of the glass and crystalline phases and the optical properties of the slags do play a role. In slag and gas entrapment, the properties which are responsible are the metal/slag interfacial tension (cmsl) and the viscosity (η). The principal factor affecting cmsl is the S content of the steel but reducing the B2O3, Na2O and CaF2 contents of the slag would help to increase cmsl.