RH degassers are lined with expensive magnesia-chrome bricks (mag chrome) to resist the corrosion by iron oxide formed due to the vacuum treatments(O2 blowing) or between treatments( O2 deskulling). Several types of magnesia chrome (magchrome) bricks are usually used in lining: direct bonded types(for vessel), rebounded types with sintered or fused co clinker(for throat and locally in up-snorkel). The life of the snorkel is typically between 130 and 200 treatments, after which the lower vessel has to be changed.
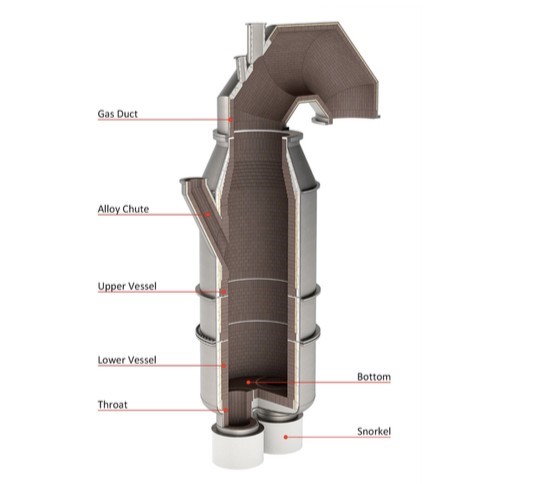
Refractory problems depend on
-Equipment: single or twin vessels, oxygen blowing tuyeres, top lance, reheating vessel device, vessel bottom cooling device, snorkel assembling system, snorkel cooling device, snorkel diameter.
-Process: argon flow rate in up-snorkel, share of standard decarb/light treatments/degassing treatments, vessel reheating TOC, ladle slag chemistry, gunning practices.
The Critical Zones for wear are:
-Snorkels:
1. Wear by corrosion-erosion of inside bricks in the up-leg(near argon tuyeres,and at the top of the throat)
2.Slag corrosion or buildup on outside
– Lower vessel lining: Wear of the lower brick courses, local holes.
Up leg: Wear takes place mostly inside the magchrome bricks. The corrosion is due to iron oxides and wear takes place by erosion in contact with fast circulating metal (near tuyerers and in upper throat). The argon flow rate, the diameter of the snorkel, gunning operations are the critical process parameters. The decrease in the metal speed in snorkels, magchrome with stronger high-temperature mechanical resistance can be useful in decreasing the wear.
Snorkels: Refractory damage mostly takes place due to thermo-mechanical problems such as due to deformation of the inside steel can, fractures of castables, inside brick slip-down, breakouts from inside or outside. This happens mostly due to overheating of snorkels(long heat series, short inter-treatments, especially at start of campaigns) The countermeasures being the cooling of snorkels(cooling system, longer inter-treatments ), stronger snorkels(thicker can, thicker bricks).
Wear of outside castables takes place by corrosion by ladle slag. The determining factors are the slag chemistry and gunning practice: CaO-rich slag (important slag carry over from converter, desulfurized heat, MnO rich slags( early addition of Mn alloys). The remedy is by decreasing the slag carryover, lime additions, and increasing outside magnesia gunning.
Outside build-up(especially down leg) takes place due to spinel deposits. The critical process parameters are slag chemistry and gunning practice-Al2O3-rich slags. The countermeasures can be by increasing lime additions and by decreasing outside gunning.
Lower vessels: Wear in the lower brick courses especially above the down-leg is due to corrosion by the action of iron oxides during treatment and by ingoing slags. The critical process parameters are OB and reoxidation rate, rate of heats with degassing of ladles with desulphurization slag. However, the rate can be decreased by decreasing the rate of such heats and fixing panels with thicker bricks.
Early breakouts can result from local corrosion, especially at joints. The critical parameters being air ingress(cracks in shell), O2 jet with bad orientation. Limiting the stress on the shell(expansion joint), control of wear of lance nose can be helpful in preventing such breakouts.
Skulling can be caused by the solidification of the metal droplets under vacuum treatment and depends on inside/outside reheating post-combustion and argon flow rate. Increasing the vessel temperature can be helpful in reducing the damage.