For well over a century the traditional method for the conversion of steel from the liquid phase to the solid phase was the use of ingot molds where each mold consists of cast iron forming a thick-walled container which is open at the top and set up before casting on large cast-iron “bottom plates” or stools.
Each ingot was cast independently and the number of ingots formed from a single ladle of liquid steel depends entirely on the ladle size and the size of each individual ingot. After the steel inside the ingot mold has solidified the ingot mold was removed using a “stripping” crane and the ingots were then charged into soaking pits so that they could be reheated for rolling to the semi-finished or finished products. Even as early as the nineteenth century, the attraction of the solidifying steel using more continuous methods was recognized and some of the methods attempted by the early workers such as G E Stellars (1840), J Laing(1843), and H Bessemer (1846) were applied to the casting of the non-ferrous metals with low melting points but not in the case of steel due to the many technical reasons associated with the high temperatures involved and the low thermal conductivity of steel. However, the possibility of solidifying liquid steel using the water-cooled mold, open at both top and bottom were pursued by R M Daelen in 1887. He envisaged a process where the stream of liquid steel was poured vertically into an open-ended mold and then passed into a secondary cooling system and withdrawn by pinch rolls prior to being cut by torch device. The process will be started by a retractable dummy bar. These features are integral parts of the modern process for the continuous casting of steel.
Early CC attempts such as the direct strip casting trials were performed by Sir Henry Bessemer in 1856. Later he implemented a stoppered tundish for slag retention. He had used a 10-by-10-inch mold beneath the tundish and a hydraulic ram was introduced to push the ingot upward for an intended direct rolling of the ingot without the use of reheating.
With growing industrialization and success of the Bessemer steelmaking process, in 1858, Swedish entrepreneur Goeran Fredrik Goeransson introduced a stoppered ladle so as to facilitate the transfer of liquid steel from the blowing vessel to the pouring pit with the help of hoist which was replaced by Henry Bessemer. in 1859 with a swing-type device known as the first ladle turret.
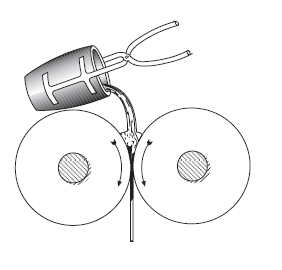
In 1885, the first ladle slide gate was conceived by David D. Lewis.
The credits for the very first machine resembling a conventional Continuous Casting (CC) machine goes to Benjamin Atha of the Atha & Illingworth Co. in Harrison, N.J., a tool steelmaker that merged into the Crucible Steel Co.of America in 1901 (together with 12 other leading special steel firms).
The first caster was built by a machine builder, i.e., Arthur McKee Co. of Cleveland, Ohio (who merged with Davy, Sheffield in 1978), had been designed by John T. Rowley of the United States Horse Shoe Co. in Erie, Pa., already with bending and unbending. The machine produced billet sizes of 45-by-45 and 75-by-75 mm in length which ranged from 10–50 m (without cut-off on the fly), but were associated with excessive mold friction that led to shell sticking and tearing at random.
However, the problem got rectified after the implementation of mold oscillation by Siegfried Junghans, the very secretive inventor, and shop manager of the renowned Black Forest clockmaking enterprise, in 1933. However, oscillating the mold up and down in order to reduce mold friction was patented by Cornelius W. van Ranst of New Rochelle, N.Y., in 1921 20 without its application at that time. The industrialization of continuous casting came into effect when engineer and businessman Irving Rossi of New York City met Junghans in1936 and he obtained his sales rights for all territories outside Germany.
A milestone in Continuous Casting from 1856 – 1950
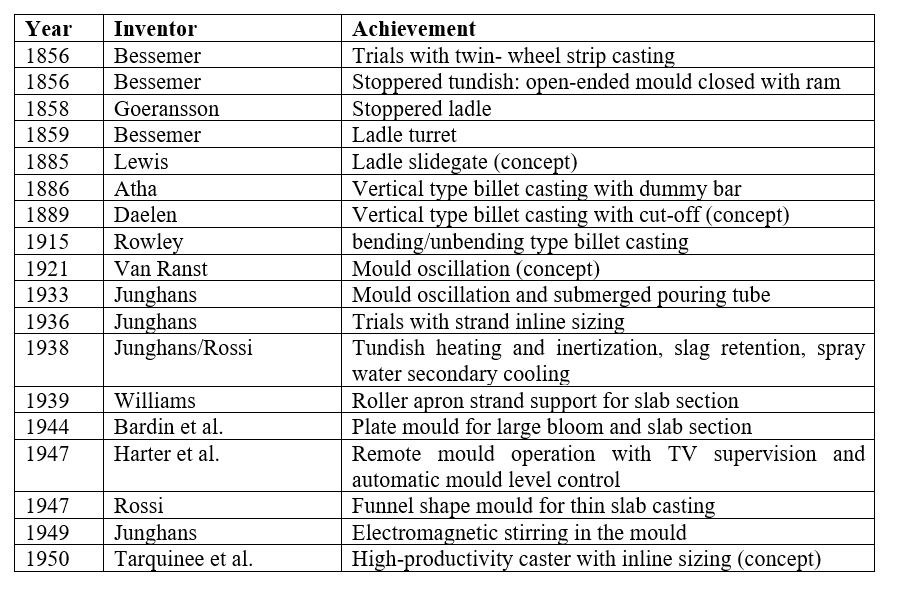
After uninterrupted caster operation for seven days, industrial application of the “Junghans-Rossi” vertical caster with mold oscillation (having a short Cu-mould length of 0.45–0.70 m, block-type having drilled water passages. These were Cr-plated and rapeseed oil was used for lubrication. These had a facility of inert gas shrouding and had oscillation stroke 12–50 mm) gained acceptance in the nonferrous industry, and a total of 12 casters were built and became operational by 1951. Five such casters were built each in Germany and the U.S. and another two in Great Britain.
Edward R. Williams, president of Vulcan Mold and Iron Co. in Latrobe, Pa., and founder of an engineering firm in 1933 made a noteworthy contribution and filed a patent application for a roller apron strand support for slab caster. Williams then teamed up with Republic Steel to start a larger pilot caster in 1942 at the Corrigan-McKinney Works in Cleveland, Ohio, for billets 100-by-100 mm as well as mini-slabs 75-by-215 mm. Additionally, in 1948 a further pilot unit was jointly built by these partners in cooperation with Babcock & Wilcox at their Beaver Falls Works, Pa. already equipped with such advanced features as automatic mold level control and remote TV supervision.
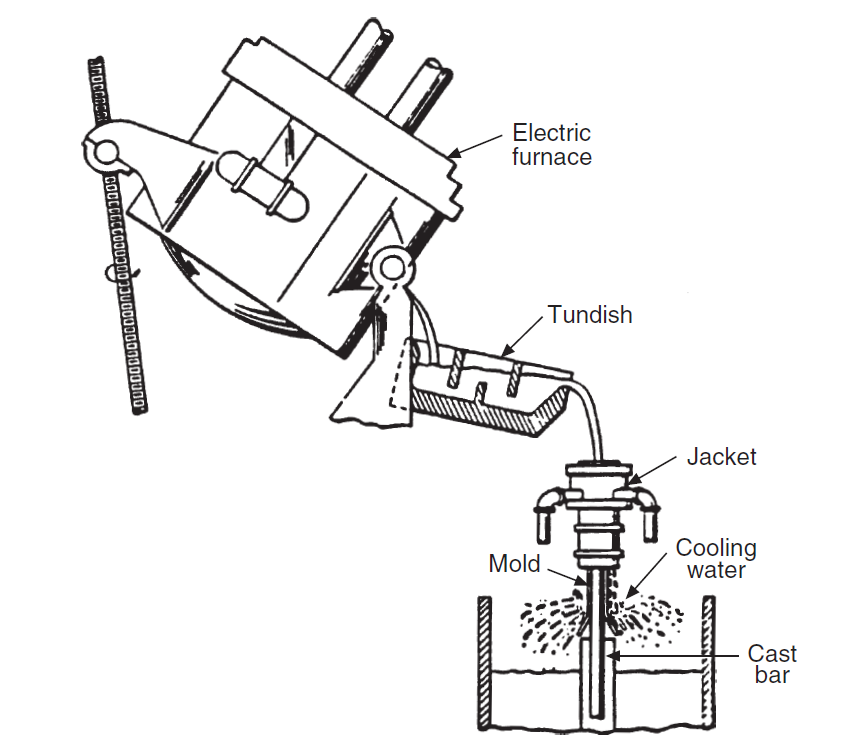
Junghans started his own pilot caster, having a one-tonne Bessemer converter at Schorndorf (1949). Later, he entered a cooperation agreement with Mannesmann, who started their pilot caster at Huckingen soon afterward (1950). In 1952, the German and Austrian CC developers joined forces, later nominating Demag as their machine builder in 1956, which led to the group’s acronym DMB, i.e., Demag-Mannesmann-Boehler.
Rossi being left alone went ahead to sell his first steel caster to Allegheny Ludlum in Watervliet, N.Y., built by Koppers Co. and started in 1949, mainly for billet sections 140 mm round and mini-slabs 75-by-380 mm. As he gave guarantees for productivity (minimum 20 tonnes per hour) and product quality, this caster machine may be considered the very first attempt at a commercial caster for steel. Apart from these features, these had additional facilities for inert gas shrouding of tundish and mold as well as resistance preheating of the (nonsubmerged) pouring tube. For the application of submerged entry nozzle (SEN) to the thin-slab section, Rossi proposed and patented a funnel-shaped dupper mold half although he did not use it.
In1950, Rossi formed the engineering company Continuous Metalcast Inc., which was registered in Wilmington, Del., in which Allegheny Ludlum and Koppers were the shareholders. Shortly thereafter, he obtained orders (mainly from specialty steelmakers) for four more casters, i.e., Atlas Steels in Welland, Ontario; Barrow Steel Works in England; NybyBruks in Eskilstuna, Sweden; and Forges d’Allevardin France.
For handling the overseas business, Concast AG in Zurich, Switzerland, was founded by Rossi in 1954. Thus emerged the two main rival groups in caster design and supply at the onset of CC industrialization,apart from many other machine-building efforts of smaller capacity. An opportunity for a certain understanding between both groups arrived after implementation of the curved mold concept when both, the DMB consortium and the Concast group, formed a joint venture company in1963 called MBC (Mannesmann-Boehler-Concast) in Zurich for mutually exploiting their patents.
In 1969, Boehler left this alliance in order to support the emerging caster business of Voest-AlpineIndustrieanlagenbau (VAI), while Mannesmann and Concast maintained their joint patent interests until 1981, when the Concast group was dismantled into solitary marketing and machine building activities of the former group members.
Vertical Steel continuous casters, 1945 to 1955
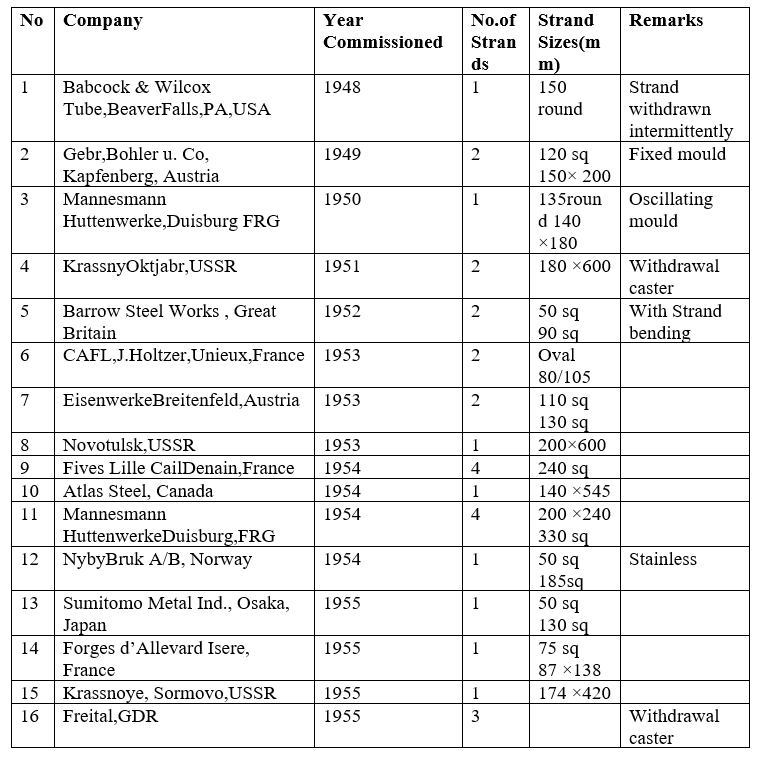
Developments during the period 1956 to 1975
The number of machines for the continuous casting of steel continued to increase steadily for the next twenty years with the following, reproduced from the second study of continuous casting by the International Iron and Steel Institute, representing important installations and developments during the period 1956 to 1975.
1956 – A vertical billet strand is bent below the pinch rolls into the horizontal plane at Barrow Steel, Great Britain( Concast/Halliday).
1958 – Slab of 1000 mm width is cast at Bohler, Austria (Mannesmann – Demag – Bohler).
1959 – An eight strand billet plant with stopper operated ladle and stopper operated tundish in Terni, Italy ( Mannesmann- Demag-Bohler).
1961- Vertical Slab caster withy bending and straightening into the horizontal in Dillingen, F.R. Germany( Concast).
1962- Introduction of casting powder at SAFE, France and Mannesmann, Germany.
The ladle turret is patented. (Concast)
Multi-purpose plant for casting either 4 slabs up to 1500 mm width or 8 blooms or 8 square or round billets at Mannesmann, Germany.
1963 – Curved caster with curve mold 200mm × 200 mm at Mannesmann, Germany.
Curved caster for billets at von Moos Stahl, Switzerland (Concast).
Centrifugal continuous casting for solid rounds at SocieteMetallurgiqued’Imphy, France(SCEC- Vallourec).
1964 – Curved caster for wide slabs at Dillingen, Germany (Concast).
Curved Caster with progressive straightening for wide slabs up to 2100 mm at Mannesmann, Germany(Mannesman- Demag). The first super low head machine(overall height 4m) of segment construction with segmented rolls.
Continuous casting of hollow rounds on a production scale at Mannesmann, Germany.
Automatic tundish stopper control system at Barrow Steel, Great Britain (Concast).
World’s first 100% continuously cast production at Shelton Iron and Steel, Great Britain.
1965- Curved caster for round strands at Eschweiler Bergwerksverein, F.R.Germany( Mannesmann- Demag).
Submerged nozzle casting at SAFE,France, and Mannesmann,Germany.
Progressive bending and straightening produced by Olson in USA.
1966- Application of ladle stream shrouding at Mannesmann, F.R.Germany.
Multi roll drive for withdrawal machine in slab caster at Mannesmann,Germany.
Tests employing the “compression casting”process at Mannesmann,Germany. Cooing plates used below the mold instead of rolls (Concast).
1967 – Strand guide section quick-change unit (oscillating table plus first segment) at Mannesmann, Germany.
Twin casting operation employing the common mold in a slab caster at Manneswar, Germany.
Greenfield steel plant in the Western hemisphere with 100% continuously cast production: Rautaruukki Oy, Finland(USSR Technology).
1968 – Production scale casting of “beam blanks” at Algoma, Canada (BISRA/ Concast technology).
LadleTurret on a continuous caster(Voest, Austria).
Hot charging of continuously cast slabs into induction furnace at McLouthSteel, USA.
Semi-industrial horizontal casters installed by General Motors, U.S.A, and Davy-Loewy, Great Britain.
1969- Tests with 120 deg C wide-angle spray nozzles at Mannesmann, Germany,(Mannesmann- Demag-Lechler).
“Permanent” dummy bar head (Concast).
1971- Application of the “compression casting” process at US Steel Gary Works, USA.
Cooling grids below the mold instead of rolls at Oxelosund, Sweden, (Concast).
Horizontal casters installed on a production scale by General Motors, Lansing, USA and Davy-Loewy, Jarrow, Great Britain.
1972 – Stepwise slab mold width adjustment during casting introduced at NSC, Hirohata, Japan.
“Walking beams” below the mold instead of rolls employed at Kobe steel, Kakogawa, Japan.
Ladle Turret with lifting system at Peine-Salzgitter, Germany(Mannesmann- Demag).
“Top fed” dummy bar system for the reduction of set up time introduced at Peine-Salzgitter, Germany(Mannesmann- Demag).
1974 – Air mist spray nozzles introduced at Mannesmann, F.R.Germany(Mannesmann- Lechler) Production scale application of EMS below the mold at SAFE, France|(SAFE-IRSID-CEM).
1975 – Production use of the pressure box to prevent reoxidation of the ladle pouring stream at Mannesmann, Germany.