HIsarna is a smelting reduction process for the production of liquid iron. It a newly developed process of iron making from iron ore fines and coal and the process eliminates the need for prior raw material processing such as agglomeration of iron ore fines and conversion from coal to coke.
In 2004, a group of European steel companies and research institutes formed ULCOS, Ultra-Low Carbon Dioxide Steelmaking and its purpose was to identify technologies that can reduce carbon emissions of steelmaking by 50% per tonne by 2050. During the period 2005-2007, cyclone technology was selected as one of the four high-potential technologies and HIsmelt technology was brought in by an agreement with Rio Tinto so as to have a win-win technology combination, which finally led to a ULCOS supported pilot plant project in Europe.
The process derives its name from the combination of two technologies HIsmelt and Isarna (‘HI’ from HIsmelt, the name of the melting vessel and ‘sarna’ from Isarna, a celtic word for iron).
HIsmelt technology has been developed by Rio Tinto and Isarna has been developed by Tata Steel in Ijmuiden. Tata Steel holds the full ownership of the patents on the HIsarna technology. The process consists of partial pre-reduction of iron ore fines in the top cyclone converter furnace (CCF) of Isarna technology and smelting of iron in the bottom smelting reduction vessel (SRV) of HIsmelt process. The process involves two-stage counter current contact between iron ore fines and the process gas.
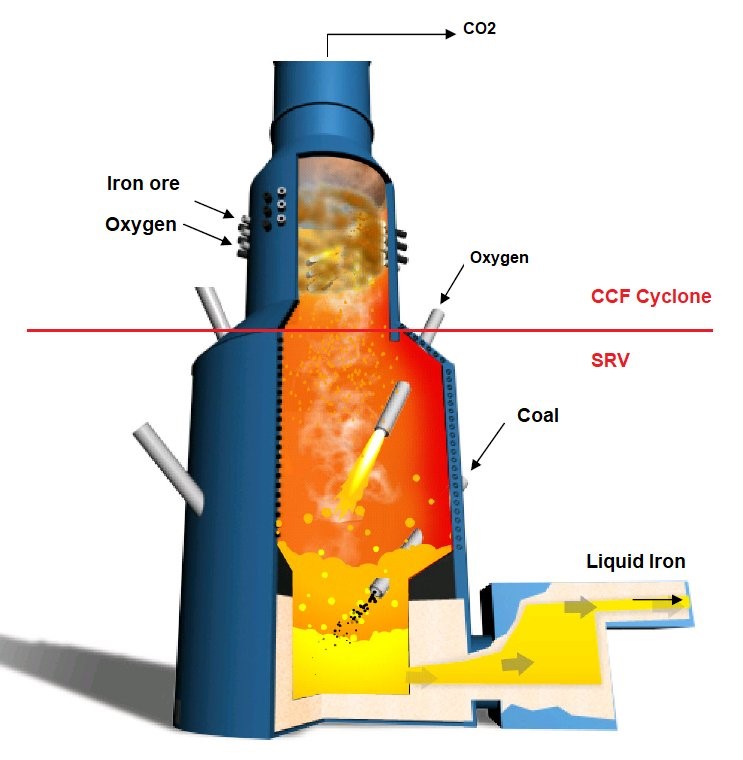
Process Description:
The vessel is shaped like a wine bottle having a bottle-shaped at the bottom and neck at the top. The geometry of the furnace gives rise to cyclone formation at the neck where the crushed iron ore is injected into this cyclone together with oxygen.
• Iron ore fines and oxygen are injected into CCF portion of the smelting vessel, where hot offgas from SRV portion of the smelting vessel is burned, leading to the partial reduction of the ore. The heat generated melts the ore. The turbulence in the cyclone provides enough contact time for the melting of the ore by hot gas. The reaction between injected pure oxygen and carbon monoxide further increases the temperature. The degree of pre-reduction is around 10-20%. The cyclone product is a mix of Fe3O4 and FeO and the fines are separated from the gas by the centrifugal flow of the gas.
• Partially reduced molten ore drips downward under the action of gravity into the SRV chamber having a temperature of around 1450 deg C . This is where the powder coal is injected at high velocity along with a carrier gas generally nitrogen, causing the oxygen from the iron ore to bind with the carbon, thus creating pure liquid iron, which can then be tapped. The metal bath contains traces of silicon and a very small percentage of manganese whereas slag contains phases of phosphorus and titanium as oxides. The main objective is to dissolve carbon which is used in the smelting step.
• Molten ore at this stage dissolves directly into the slag. The agitation created by the coal injection plume helps in slag metal mixing which in turn creates a large metal slag interfacial area for smelting. Dissolved carbon in the metal reacts with the oxygen of the ore and a significant amount of CO gas is formed. This reaction being highly endothermic requires a heat source to keep this part of the vessel in balance. This takes place in the lower part of the vessel. The mixing helps in the reduction of FeO content in the slag, which is typically around 5-6%. The iron oxide in the slag is reduced at the slag/metal interface.
•The upward movement of gases such as CO gas from smelting, along with conveying gas (nitrogen) and the devolatilization products of coal constitutes generates a large amount of splash, resulting in droplets formation due to the cycling of metal and slag in the upper portion of the smelting vessel. Heat is generated due to combustion by the introduction of oxygen through lances. The heat generated is carried over by these droplets from the upper region to the lower region of the smelting vessel. The partly burnt gas from the smelting vessel provides the hot fuel gas for the cyclone part of the vessel.
Before the start of each testing campaign, the reactor is preheated to a temperature of about 1,200 deg C followed by the introduction of a layer of liquid iron into the bottom of the melting vessel, in order to facilitate the start-up of the process.
Advantages of the process:
· Lowers process costs due to 20% savings in primary energy consumption.
· 20% reduction of CO2 emissions without CCS (CO2 capture and storage).
· Well suited for CO2 storage (Nitrogen free off the gas)
· 80% reduction of CO2 emissions with CCS.
· 60% to 80%reductions in other emissions (dust, NOx, SOx, CO)
· There is increased flexibility of raw material usage.
· Enables a more resource-efficient process as ores with substantial P, Zn, alkalis and S content can even be used.
Initial Trial Performance
HIsmelt was originally started in the 1980s by CRA (now Rio Tinto) in a 2 tph pilot plant at Maxhutte, Germany followed by 8 tph pilot plant in Kwinana, Western Australia in 1990s.
Pilot plant was started during April 2011 and was operated from 18 April to 11 June 2011 in its first campaign. There were five campaigns that ran over a span of six years. The first startup was unsuccessful but the second campaign which ran 17 October to 4 December 2012 was able to produce liquid iron for a longer, sustained period and achieved production at 80% of design capacity for periods of 8 to 12 hours. The last run was able to achieve the design capacity of 8 tph.
After the successful trials, Tata Steel now intends to set up the first scaled-up plant in India, and subsequently, build a commercial plant in Ijmuiden.