The tundish slide gate like the stopper rod functions to control the metal flow from the tundish to the mold. The slide gate mechanism consists of an upper nozzle placed inside the well block, top plate, sliding middle plate, and bottom plate essentially with a collector nozzle for placement of the submerged entry nozzle. The bore diameter varies from 40 to 50 mm depending on the throughput required. The system is sealed with the help of argon (provision for argon sealing is provided on the bottom and top plates which also serves for the cooling of the plates). The housing is provided with a spring to keep the plates under compression. Many tundish slide-gate systems require air cooling for the springs that supply sealing force to the plates. A glass fiber rope is added which acts as a mechanical seal between the main frame and the top plate.
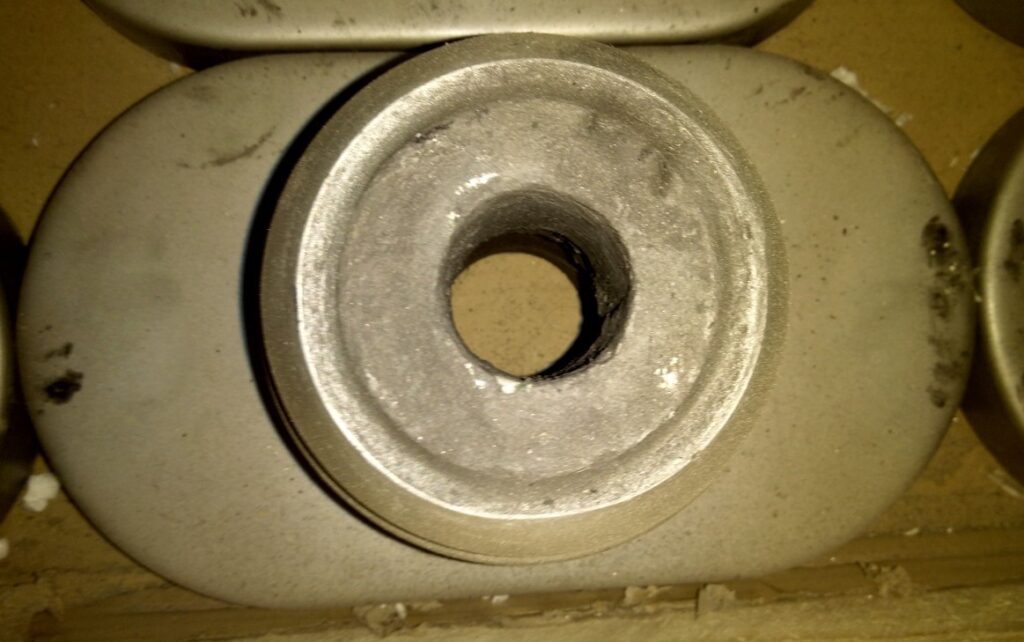
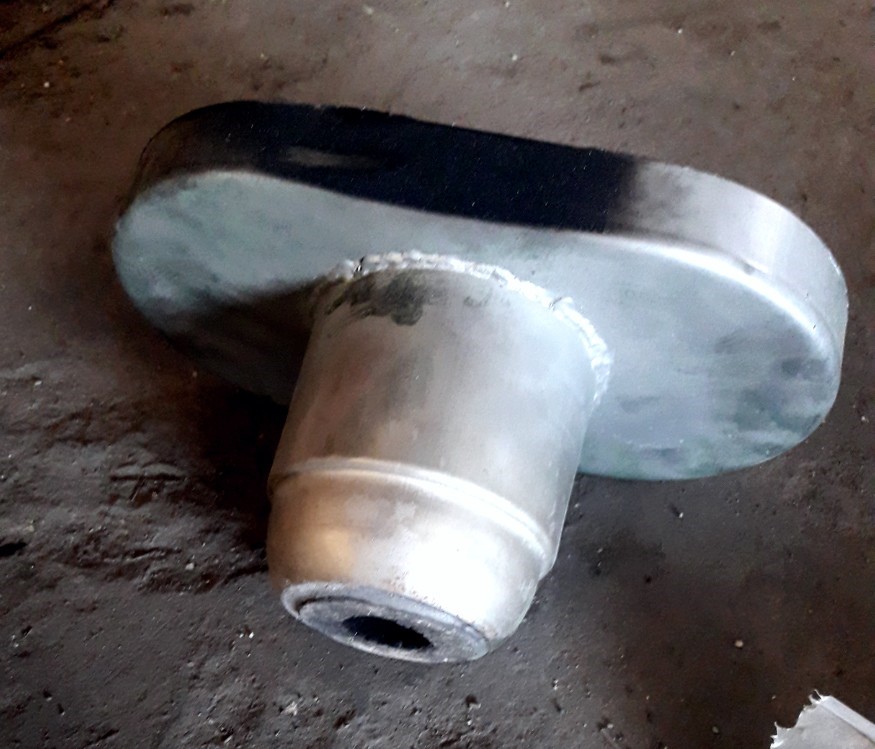
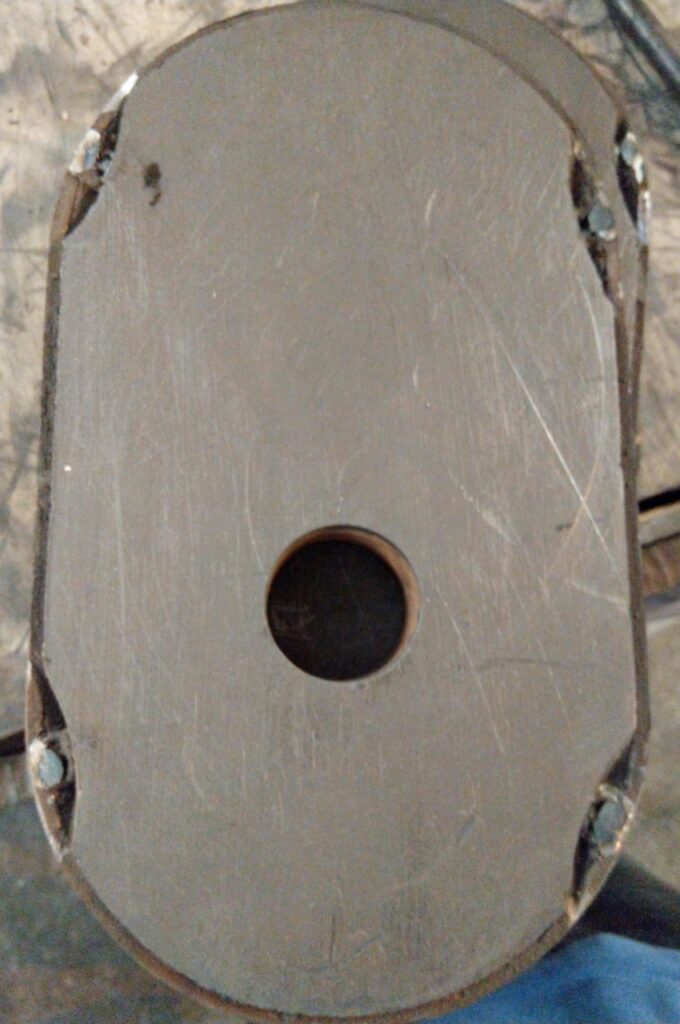
Thermal
Peak Temperature: The plates in contact with steel reaches the steel temperature. The temperature is very high from the refractory point of view and very high-temperature material is preferred.
Thermal Shock: The thermal cycling for the working lining is considerably high. The lower plate experiences greater shock being in the open air and when the gate is opened and steel flows through it. The thermal shock is accentuated by the presence of cold argon, primarily used for cooling and sealing induces thermal stress when it comes in contact with the hot refractory.
Mechanical
Impact: The impact is low.
Abrasion: The abrasion is dependent on the throughput of steel and the size of the bore. The size of the bore is important as far as the abrasion is concerned. When the bore diameter is large then the overlap of the will be small leading to more turbulence and force generation on the lower plate. But when the overlap is more when the bore size is small it becomes harder to control metal flow or compensate for any chocking in the nozzle. The recommended overlap is 50 % for the desired output. Additionally, the movement of plates causes further wear which is not the case for the tundish upper nozzle.
Applied Stress: The applied stress is high for the plates. They need to be kept under the action of compressive stress due to the need to prevent metal leaking from the plate gap and prevent propagation of cracks. The presence of argon cooling and sealing puts additional stress on the plate.
Chemical
Dissolution: Wear by dissolution depends on the chemical compatibility of the slags with bricks. The Ca vapour attack is a major issue when casting special grades of steel containing Ca which is in added to modify flow inclusions. When Ca is present is present in the steel and there is overlap of steel plates the calcium gets converted to Ca vapour and reacts in an aggressive manner due to the presence of alumina in the plates. This causes severe wear especially when the concentration of Ca crosses 40 ppm. The wear is in the shape of horse shoe due to the shape it attains after service. MgO or MgC can be alternate solution but it suffers from thermal shock/spalling due to the expansion rate and the stress.
Penetration: Penetration is caused by low viscosity metal/ slag or highly wetting metal/slag penetrating into porous refractories. Oxygen lancing is generally not done and the chance of low viscosity slag formation is rare.
Thermo- Mechanical
Strain of thermal expansion– The applied stress is high for the plates. They need to be kept under the action of compressive stress due to the need to prevent metal leaking from the plate gap and prevent propagation of cracks. The presence of argon cooling and sealing puts additional stress on the plate.
Chemical Mechanical and thermo mechanical chemical
Spalling of the penetrated zones- The application of applies stress along with abrasion from metal flow, thermal stress due to cold argon flow, corrosion by Ca vapor reduces the life of the plates abruptly.
Choice of material
Slide gate: The slide gate plate is made up of alumina- carbon mix of 20-25% C (94% graphite) and 70-75 % alumina (tabular fused alumina with mullite additions). Sometimes 0-5% Zirconia is added. Antioxidants like Al, Si is added to protect the carbon.
Tundish upper nozzle: The material used can be alumina or alumina spinel or pure magnesia or alumina carbon mix with zirconia. High purity material are normally preferred because the material has to sustain really high temperatures.
The top nozzle is the key wear area and contains zirconia or spinel or magnesia if high calcium grades are cast. The body generally consists of single material depending on the grade mix.
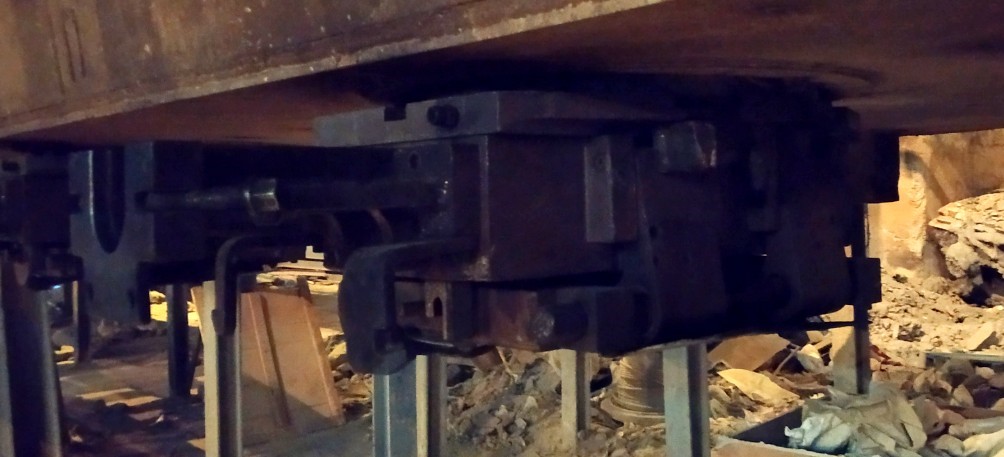
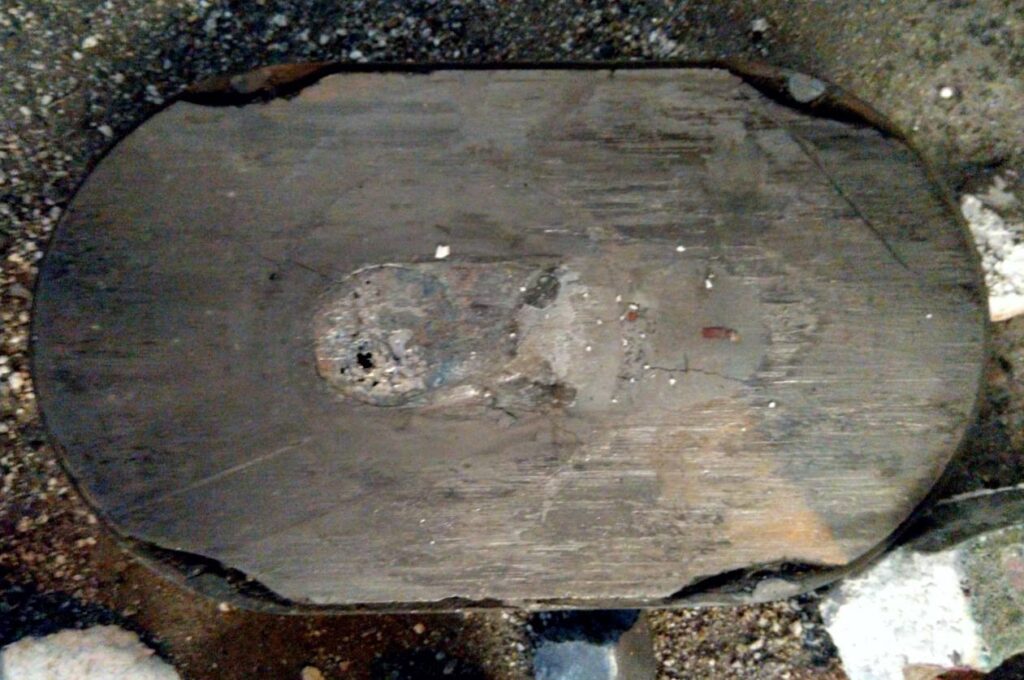